What is Porosity in Welding: Recognizing Its Causes and Enhancing Your Abilities
Wiki Article
The Scientific Research Behind Porosity: A Comprehensive Guide for Welders and Fabricators
Comprehending the intricate systems behind porosity in welding is vital for welders and fabricators pursuing flawless craftsmanship. As metalworkers dive right into the depths of this phenomenon, they discover a world regulated by numerous elements that influence the formation of these tiny gaps within welds. From the make-up of the base materials to the ins and outs of the welding procedure itself, a plethora of variables conspire to either intensify or minimize the visibility of porosity. In this thorough overview, we will unravel the scientific research behind porosity, discovering its impacts on weld quality and introduction advanced strategies for its control. Join us on this trip with the microcosm of welding imperfections, where precision fulfills understanding in the quest of remarkable welds.Understanding Porosity in Welding
FIRST SENTENCE:
Assessment of porosity in welding exposes vital understandings into the stability and quality of the weld joint. Porosity, characterized by the visibility of cavities or gaps within the weld steel, is a common concern in welding procedures. These gaps, if not correctly dealt with, can jeopardize the architectural honesty and mechanical buildings of the weld, leading to prospective failures in the completed product.
To spot and evaluate porosity, non-destructive screening approaches such as ultrasonic screening or X-ray evaluation are usually used. These techniques permit for the recognition of inner flaws without jeopardizing the integrity of the weld. By evaluating the size, form, and distribution of porosity within a weld, welders can make enlightened choices to improve their welding processes and attain sounder weld joints.
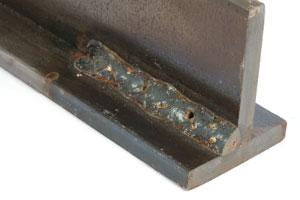
Variables Affecting Porosity Formation
The occurrence of porosity in welding is affected by a myriad of aspects, varying from gas shielding performance to the intricacies of welding specification setups. Welding criteria, including voltage, current, travel rate, and electrode kind, additionally influence porosity development. The welding method used, such as gas steel arc welding (GMAW) or protected metal arc welding (SMAW), can influence porosity formation due to variations in warmth distribution and gas insurance coverage - What is Porosity.Effects of Porosity on Weld High Quality
Porosity formation substantially endangers the structural integrity and mechanical properties of bonded joints. When porosity is existing in a weld, it produces voids or cavities within the material, lowering the general strength of the joint. These gaps act as stress concentration points, making the weld much more vulnerable to fracturing and failure under lots. The existence of porosity also weakens the weld's resistance to deterioration, as the caught air or gases within deep spaces can respond with the surrounding atmosphere, causing deterioration gradually. In addition, porosity website link can hinder the weld's ability to hold up against pressure or effect, more jeopardizing the total quality and dependability of the welded structure. In important applications such as aerospace, auto, or structural buildings, where safety and longevity are vital, the destructive results of porosity on weld high quality can have severe consequences, highlighting the relevance of reducing porosity with appropriate welding techniques and treatments.Techniques to Minimize Porosity
In addition, utilizing the suitable welding specifications, such as the right voltage, existing, and travel rate, is important in avoiding porosity. Preserving a constant arc size and angle during welding additionally helps lower the possibility of porosity.
Moreover, choosing the ideal securing gas and keeping appropriate gas circulation prices are vital in reducing porosity. Making use of the proper welding method, such as back-stepping or utilizing a weaving movement, can likewise assist distribute warmth equally and minimize the opportunities of porosity development. Guaranteeing appropriate ventilation in the welding environment to eliminate any type of possible sources of contamination is important for accomplishing porosity-free welds. By implementing these techniques, welders can efficiently minimize porosity and generate high-grade welded joints.
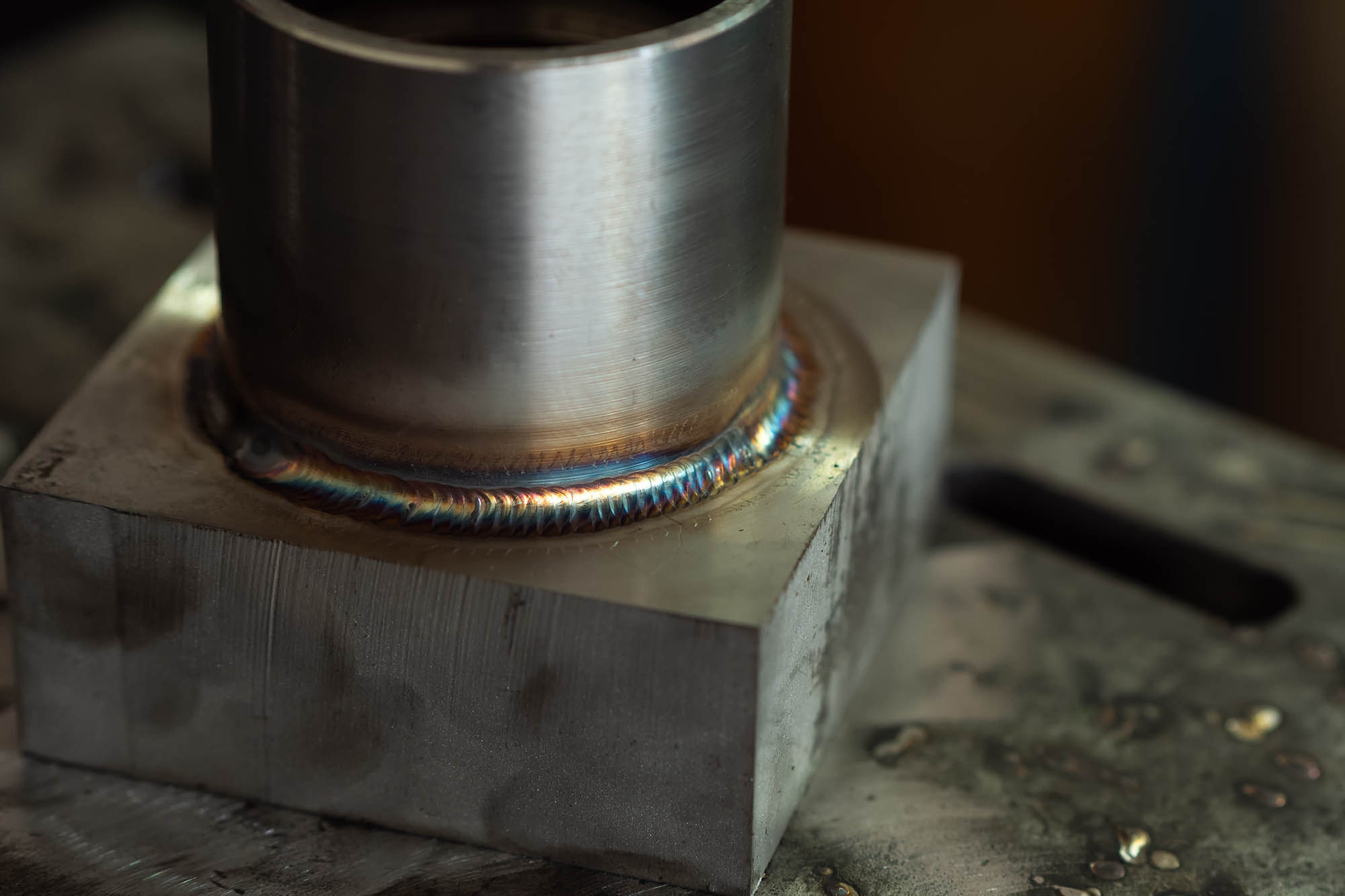
Advanced Solutions for Porosity Control
Carrying out innovative technologies and innovative approaches plays a crucial duty in attaining superior control over porosity in welding processes. One Resources sophisticated remedy is using advanced gas mixtures. Protecting gases like helium or a blend of argon and hydrogen can help in reducing porosity by offering far better arc security and enhanced gas coverage. Furthermore, utilizing sophisticated welding techniques such as pulsed MIG welding or customized atmosphere welding can also help alleviate porosity problems.One more advanced option involves making use of innovative welding equipment. Utilizing devices with integrated functions like waveform control and innovative power sources can boost weld top quality and reduce porosity threats. Additionally, the implementation of automated welding systems with specific control over parameters can dramatically decrease check my source porosity flaws.
Furthermore, including sophisticated tracking and inspection innovations such as real-time X-ray imaging or automated ultrasonic testing can help in spotting porosity early in the welding process, permitting instant rehabilitative actions. Overall, incorporating these sophisticated options can substantially enhance porosity control and improve the total top quality of bonded elements.
Verdict
To conclude, understanding the scientific research behind porosity in welding is important for welders and makers to produce high-grade welds. By recognizing the aspects affecting porosity development and implementing techniques to minimize it, welders can boost the overall weld top quality. Advanced services for porosity control can further boost the welding process and guarantee a strong and dependable weld. It is necessary for welders to constantly inform themselves on porosity and implement best practices to accomplish optimum outcomes.Report this wiki page